Introduction Molded Plugs
In various industries, from paper manufacturing to packaging, efficient and reliable core plugs are essential. Molded roll & tube paper core plugs offer a sustainable and cost-effective solution. This article delves into the materials, applications, and production equipment behind these versatile components.
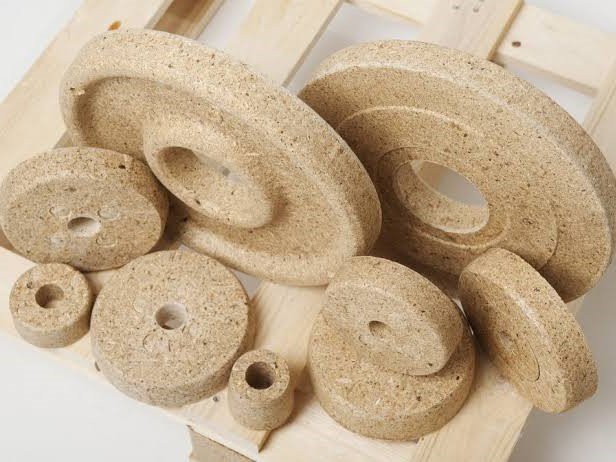
What are Molded Roll & Tube Paper Core Plugs?
Molded roll & tube paper core plugs are end caps or plugs inserted into the ends of paper cores or tubes. They provide stability, prevent damage during handling and shipping, and ensure consistent winding and unwinding of materials. Unlike traditional plastic or metal plugs, molded plugs are typically made from recycled wood fibers, making them an environmentally friendly choice.
Raw Materials: Utilizing Recycled Wood
A key advantage of molded core plugs is their sustainable composition. The primary raw materials include:
- Wood Chips and Sawdust: These byproducts of the lumber industry are readily available and provide excellent structural integrity.
- Recycled Wood Fiber: Utilizing recycled wood further enhances the environmental benefits and reduces waste.
These materials are processed and mixed with binding agents to create a moldable compound.
Applications Across Industries
Molded roll & tube paper core plugs find wide application in various sectors:
- Paper and Film Industry: Used in rolls of paper, film, and other rolled materials to prevent telescoping and damage during storage and transport.
- Textile Industry: Used in yarn and fabric rolls to maintain shape and prevent unraveling.
- Packaging Industry: Used in packaging tubes and cores for various products.
- Other Industries: Including tape manufacturing, label production, and more.
The Production Process: Press Molding Technology
The manufacturing of molded core plugs relies on press molding machines:
- Material Preparation: The wood fibers are processed, dried, and mixed with binding agents.
- Molding: The mixture is placed into molds and subjected to high pressure and heat in a press molding machine. This process forms the desired shape and provides strength and durability.
- Finishing: The molded plugs are cooled, trimmed, and inspected for quality control.
Advantages of Molded Core Plugs
- Sustainable and Eco-Friendly: Made from recycled wood, reducing waste and environmental impact.
- Cost-Effective: Often more economical than plastic or metal alternatives.
- Durable and Strong: Provide reliable support and protection for rolled materials.
- Customizable: Can be molded in various sizes and shapes to meet specific requirements.
- Biodegradable: An environmentally responsible disposal option.
Conclusion
Molded roll & tube paper core plugs offer a sustainable, efficient, and cost-effective solution for various industries. Their use of recycled materials and efficient production processes make them an attractive choice for businesses seeking environmentally responsible and high-performing components.
Contact us today to learn more about our range of molded core plug solutions.