Pallets play an indispensable role in safely transporting goods in logistics and supply chain management. With the growing demand for more sustainable and cost-effective packaging solutions, molded pallets have emerged as a popular alternative to traditional wooden pallets. These Presswood pallets are made from recycled materials, such as waste wood waste wood scraps, and other farming waste. They are becoming the preferred choice for many industries due to their durability, environmental benefits, and cost-efficiency.
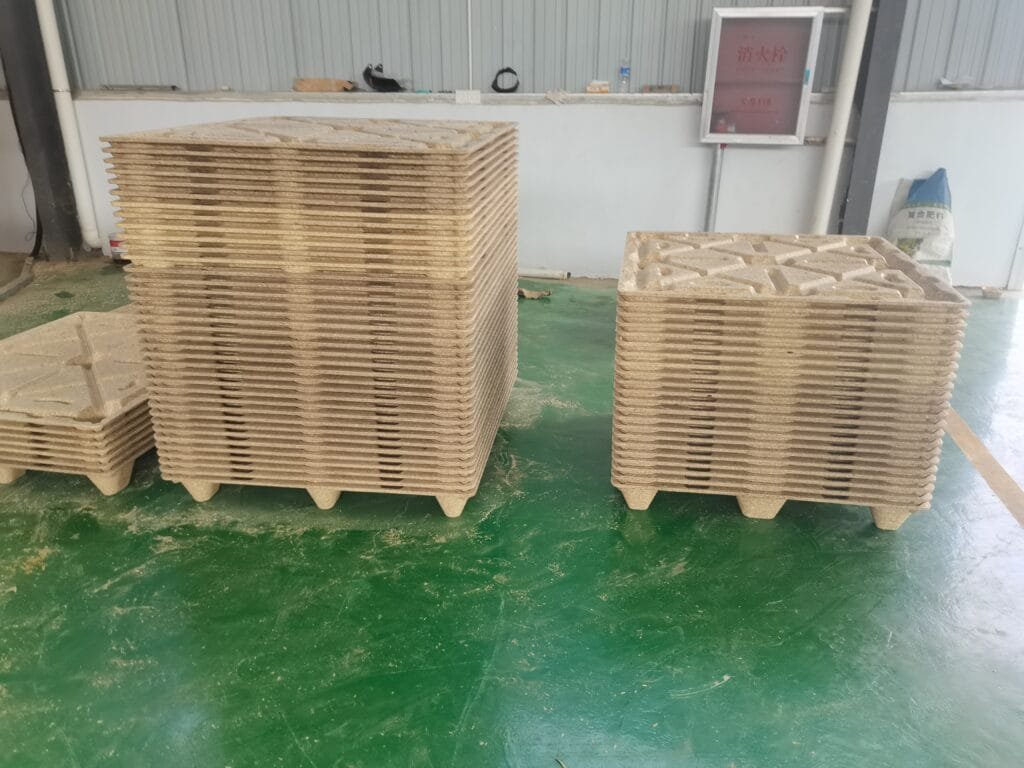
In this article, we will explore the step-by-step process of producing compressed pallets using cutting-edge pallet molding machines and explain why these products are revolutionizing the packaging industry.
Step 1: Sourcing and Preparing Raw Materials
The journey of creating a presswood pallet begins with the sourcing of waste wood and waste wood scraps. Instead of using freshly cut timber, these materials are collected from wood processing industries, construction sites, and even sawmills. This method not only reduces the demand for new wood but also helps reduce the environmental impact of waste disposal.
Approximately 60% of the raw material used in molded pallets comes from recycled wood products, making them an environmentally friendly alternative. By using waste wood, we are contributing to reducing deforestation and promoting the circular economy.
Step 2: Shredding and Chipping the Waste Wood
Once the waste wood is collected, it is first shredded and chipped into smaller pieces. These wood chips are then processed further to ensure uniformity in size, chips size 5mm to 15mm is the best. The wood chips are essential for the next stage, as they will be transformed into the final pallet form through compression.
The precise size (5mm-15mm) and quality of the chips are crucial to the final product’s strength and durability. The process also helps eliminate any contaminants in the wood, ensuring the compressed pallets are free from harmful chemicals and impurities.
The chips must be dried to make sure the moisture content is less than 8%, 5% is the best.
Step 3: Mixing with Resin and Molding
After the wood chips are prepared, they are mixed with a special resin and pressed together in a pallet molding machine. The resin serves as a binding agent, holding the wood particles together and providing the necessary strength and flexibility.
The presswood pallet machine then molds the mixture under high pressure 21MPa, typically at around 150-180°C, to form the desired shape of the pallet. The temperature and pressure are carefully controlled to ensure the final product is both sturdy and lightweight. This process creates a compressed pallet that is highly resistant to wear, weather, and termites.
*Resin: UF, MUF, MDI
Resin Ratio: UF=12-15%,
MUF=12-15%,
MDI=5%
Step 4: Drying and Cooling
After the molding process is complete, the newly formed presswood pallets are placed in drying chambers. Here, they are exposed to controlled temperatures and airflow to remove any remaining moisture. This step ensures the pallets achieve their optimal strength and prevents warping during use.
The drying process typically lasts between 3 to 5 hours, depending on the size and thickness of the pallet. Once dried, the pallets are cooled down to room temperature, and ready for inspection.
Step 5: Quality Control and Final Inspection
Before the molded pallets are shipped out, they undergo a rigorous quality control check. Each pallet is inspected for defects such as cracks, uneven surfaces, and structural integrity. The presswood pallet must meet industry standards for load-bearing capacity and durability. Typically, a presswood pallet can hold up to 1,500 kg (3,300 lbs), making it suitable for heavy-duty applications.
In addition, the final inspection includes a check for moisture content, which should be less than 12%. This ensures that the pallets will perform well in various environmental conditions, from humid warehouses to dry shipping containers.
Step 6: Packaging and Shipping
Once approved, the compressed pallets are packaged and prepared for shipment. The pallets are typically stacked and wrapped to ensure they remain in good condition during transportation. Some manufacturers also offer customized packaging solutions to fit specific client needs, including the ability to create different sizes and shapes of pallets.
Why Choose Molded Pallets?
- Sustainability: By using waste wood and waste wood scraps, molded pallets offer an eco-friendly alternative to traditional wood pallets. This helps conserve natural resources and reduces the environmental impact of waste disposal.
- Durability: The compression process creates a highly durable product that resists breakage, moisture, and pests. Presswood pallets are also lightweight, which reduces shipping costs.
- Cost-Effective: Since molded pallets are made from recycled materials, their production costs are often lower than traditional pallets, making them an attractive option for businesses looking to save money while remaining environmentally responsible.
- Customization: The pallet molding machine allows for a high degree of customization. Manufacturers can adjust the mold to create pallets in different sizes, shapes, and designs, catering to the specific needs of their clients.
- Space Saving: 42pcs – 45pcs pallets stacking 2 meters high. one 20 feet dry container can fill about 450 pcs pallets size 1200x1000mm, one 40 feet dry container can fill about 1150 pcs pallets size 1200x1000mm.
Conclusion: A Smart and Sustainable Choice
The production of molded pallets represents a significant advancement in the packaging industry. With the use of presswood pallet machines, businesses can create strong, durable, and eco-friendly pallets that are not only cost-effective but also contribute to the sustainable use of resources. By opting for compressed pallets, companies can reduce their environmental footprint while ensuring safe and reliable transportation of goods.
If you’re interested in learning more about how molded pallets can benefit your business, feel free to contact us today. Our team of experts is ready to assist you with any inquiries about our presswood pallet machines and custom pallet solutions.