In the production of molded wood pallets, mold temperature plays a critical role in determining both the quality of the final product and the efficiency of the manufacturing process. This article delves into why heating the mold is essential, the equipment used for heating, and the optimal temperature range for production. Additionally, we will explore how mold temperature interacts with other key factors such as press pressure, mold design, and adhesive type to influence the overall outcome.
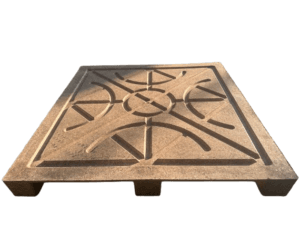
Why is Heating the Mold Necessary in Molded Wood Pallet Production?
- Curing of Thermosetting Adhesives
Molded wood pallets are produced using thermosetting adhesives such as Urea-Formaldehyde (UF), Phenol-Formaldehyde (PF), and Methylene Diphenyl Diisocyanate (MDI). These adhesives require heat to activate and cure properly. For instance:- UF resin typically cures at 120°C to 140°C.
- PF resin may require temperatures above 160°C.
- MDI adhesives generally operate within a range of 130°C to 180°C.
Proper heating ensures the adhesive bonds effectively with the wood fibers, resulting in a durable and stable pallet.
- Improved Wood Fiber Plasticity
Heating the mold enhances the plasticity of wood fibers, allowing them to conform more easily to the mold’s shape. This results in better surface finish, higher strength, and improved dimensional stability of the pallet. - Increased Production Efficiency
Optimal mold temperature accelerates the curing process, reducing cycle times and increasing throughput. Insufficient heating can lead to incomplete curing, longer production times, and higher defect rates. - Compliance with International Standards
According to the International Plant Protection Convention (IPPC), wooden packaging materials, including pallets, must undergo heat treatment to eliminate pests and pathogens. Heating the mold to the required temperatures ensures compliance with ISPM 15 standards, allowing the pallets to be used in international trade without additional treatments like fumigation.
Equipment Used for Heating Molds
Several heating methods are commonly used in molded wood pallet production:
- Mold Temperature Controllers (Oil-Based)
These systems use thermal oil as a heat transfer medium. The oil circulates between the mold and the controller, ensuring consistent and efficient heating. Mold temperature controllers are compact, easy to operate, and ideal for single-press setups. - Thermal Oil Boilers
Thermal oil boilers provide centralized heating for multiple presses. While they offer efficient heat distribution and management, they require dedicated space for installation and extensive piping. A boiler malfunction can halt the entire production line. - Steam Boilers
Steam boilers use superheated steam to heat the molds. Like thermal oil boilers, they are suitable for centralized heating but come with similar drawbacks, including the need for dedicated infrastructure and vulnerability to system-wide failures. - Electric Heating Systems
Electric heating elements, such as heating rods or coils, are directly integrated into the mold. This method offers rapid heating and precise temperature control, making it suitable for small-scale or precision production. However, it can be energy-intensive and less cost-effective for large-scale operations.
Optimal Mold Temperature for Pallet Production
The ideal mold temperature for producing molded wood pallets typically ranges between 150°C and 180°C. This range balances several factors:
- Efficiency: Higher temperatures speed up the curing process, improving production rates.
- Quality: Excessive heat (above 210°C, the ignition point of wood fibers) can cause surface discoloration or charring, compromising the pallet’s appearance and structural integrity.
- Curing Depth: Pallets with wall thicknesses of 10mm to 15mm require sufficient time for heat to penetrate the core. Even after removal from the mold, the pallet continues to cure, reaching optimal strength after 2 to 24 hours of cooling.
Other factors impact the presswood pallet production: Factors Affecting the Output of Molded Wood Pallet Production Line
Key Factors Influencing Pallet Quality and Production Efficiency
While mold temperature is crucial, it works in conjunction with other factors:
- Press Pressure: Higher pressure ensures better compaction of wood fibers and adhesive, enhancing the pallet’s strength and durability.
- Mold Design: Well-designed molds facilitate even heat distribution and efficient material flow, reducing defects and improving consistency.
- Adhesive Type: The choice of adhesive (UF, PF, or MDI) affects curing time, bond strength, and overall performance. For more details, refer to our article: Glue For Molded Pallet Production
Conclusion
In molded wood pallet production, maintaining the right mold temperature is essential for achieving high-quality products and efficient manufacturing. By combining optimal heating with well-designed molds, appropriate press pressure, and the right adhesive, manufacturers can ensure compliance with international standards, reduce production costs, and deliver durable, reliable pallets.
For industry-leading expertise in molded pallet machinery, mold design, and production solutions, consider partnering with WATTMECH, a pioneer and leader in the field. Contact them today for consultations or customized quotes tailored to your production needs.